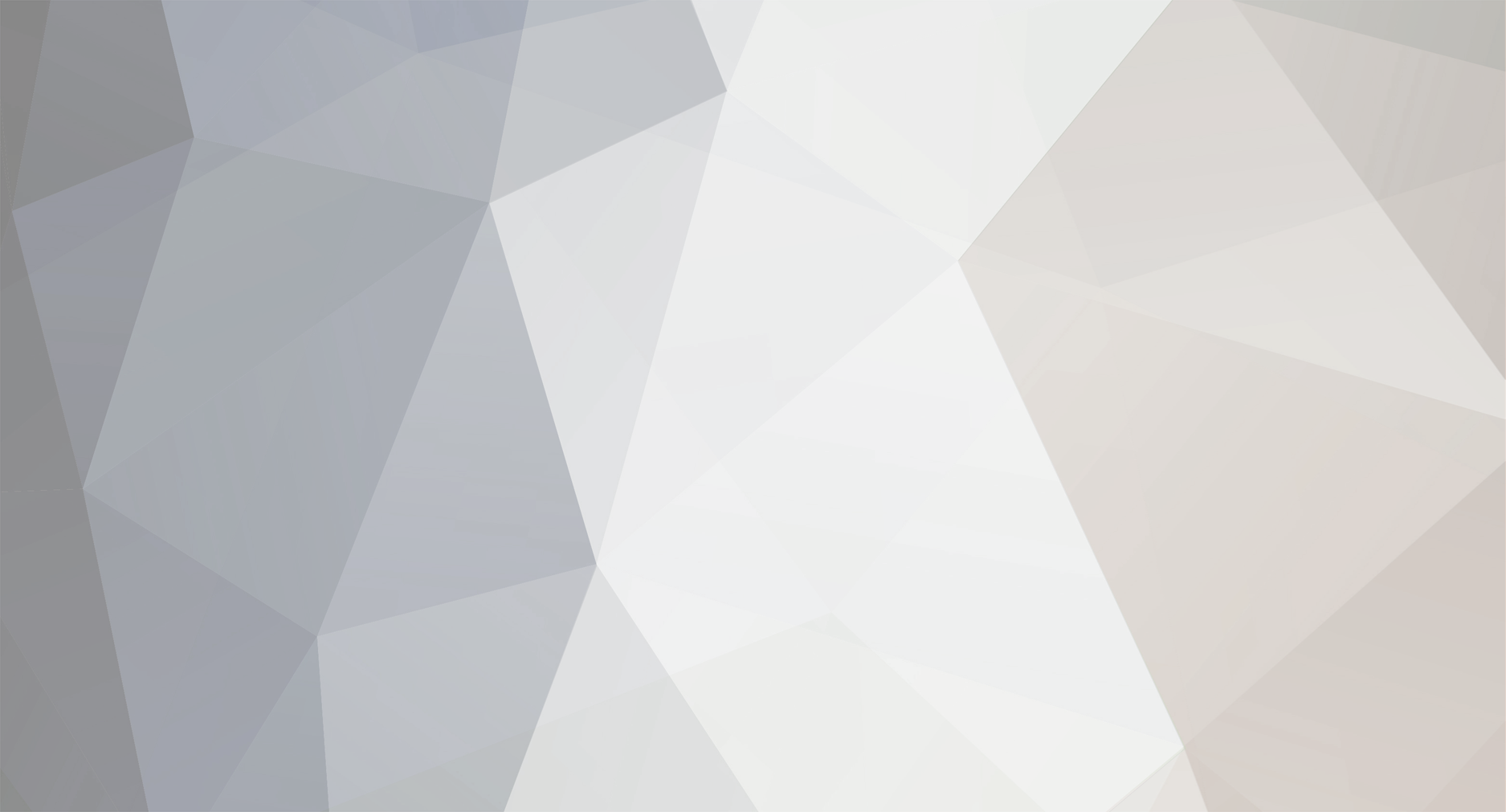
Balleristic31
New Members-
Posts
19 -
Joined
-
Last visited
Profile Information
-
Location
Los Angeles, CA
-
Cars
1969 Datsun 510, 1991 BMW 318is Turbo
Recent Profile Visitors
The recent visitors block is disabled and is not being shown to other users.
Balleristic31's Achievements
Newbie (1/14)
62
Reputation
-
Another big update today! First, we picked up a roll bar a few months back from a gentleman who builds them out here in LA. It still needs a harness/cross bar welded in, but Dad fitted/painted/installed it for now. Below you can see a few pictures of the mock up/test fit. Then the bar was painted body color and installed! Also here you can see the rear side windows installed and the b-pillars all painted up with SEM trim paint to match the window frames. This is one of my favorite photos of the car thus far. Here you can also see the rockers painted black as well. Door panels were installed. Interior is really coming together now! Mirrors holes were carefully mocked up and drilled. Sorry everyone, no JDM mirrors on this 510! Unfortunately, when the car was pulled out of the garage the wind picked up and tossed the rear window off the roof completely destroying it. Luckily, the 510 community is awesome and we had a new window (thanks Seth!) within a day or so! And the brand new windshield installed! With all the glass installed, it was time to finally take the car on its first real trip to the gas station. Please enjoy the photos below, as they are a culmination of over a year’s hard work by Dad! And one final shot this morning. Looks fantastic in the sun!
-
Big update for everyone! As of a couple weeks ago, the car runs and drives under its own power! The car basically fired right up after plumbing the remainder of the fuel system and buttoning up a few small items. No video of the first start right now, but we have something better: a flyby! Listen to that induction noise! The 18RG runs very strong even with a slight lean condition at the moment. There is a bit of oil burning, and the transmission is a bit noisier than we were hoping it would be, but its quick! The torque of the 2.0L is lovely. Keep in mind this car hasn’t moved under its own power in over 20 years! Beyond getting it running, additional miscellaneous progress has been made across the entire car. The front end was assembled including the front valence, airdam/lip, bumper and the grill assembly. A few BRE touches/decals were added. Definitely fits the character of the car in my opinion! At some point before the gas tank went back in, the trunk was also painted body color to match the rest of car. The valve cover was pulled for its coating in VHT wrinkle black. Some strategic masking/sanding afterwards led to a stealthy look that aids in hiding the true identity of the powerplant. And installed. These photos really illustrate how far this engine bay has come. Below I posted some of the engine bay shots when the car was first purchased for comparison. Dad did an absolutely fantastic job on this build and it really shows. I’ll leave it here for now. Roll bar/interior updates to come shortly!
-
Ted this is so badass!! Thank you for sharing!! It's really cool to see that car/all the rest running. This was all before my time! :D
-
Once the wiring was all set, we could finally do a finished assembly on the dash panel. Before that could take place, the dash and rear seat delete panels need to be coated with the previously chosen wrinkle black finish. Initially we were going to use VHT spray and work the wrinkles in manually with a heat gun, but after a bit of deliberation we determined powder coating would be a much better and more durable option. The end result was very satisfying and looks fantastic! First the rear panels were mocked up in their final position. Looking good! Then came the upper dash panel. And finally, the front face of the dash. Fantastic! Installed! And here are a few pictures of the backside of the dash panel all tidied up. All in all, we are thrilled with how the dash came together. It’s starting to look like a car again!
-
Time for an update! Dad has been working extremely hard to finish up the wiring and we are beginning to inch closer and closer to that first drive! This part of the project was extremely daunting, but with patience and the well labeled/designed Painless wiring kit, the overall process was…. relatively painless. We wanted the dash panel to be 100% removable and serviceable so the wiring harness attached to all the gauges and switches had to be on a separate loom. Below was a relatively early mock-up of some of the wiring. Once the location of the fuse box and relays were roughly determined, the dash harness was slowly put together. And ended up looking like this! Looking great! All connections were crimped/soldered and shrink wrapped. A couple power and ground distribution blocks were then mounted to the dash support. Once the dash harness was created the body harness was formed. Dad made a bulkhead connector to separate the dash harness from the main harness and fuse box for serviceability. You can see where that harness spits out of the firewall here next to the fusebox. And then the remainder of the inside body harness. And here you can see the engine bay harness where it comes through the firewall. A power junction block included in the Painless kit was mounted to the passenger side firewall. Here you can see all of the starter wiring. The front lights, ignition, and alternator wiring come out of the inner fender well and into the engine bay on the passenger side. Looking awesome! This was a ton of work and I really think the wiring came out fantastic and exceeded expectations. Many hours went into this harness and it really shows.
-
Tackling the exhaust was high on the priority list while the car was up in the air on jack stands. The exhaust that came on the car was basically junk so we scrapped everything rearward of the header collector. After cutting/shaping/ fitting repeatedly, we ended up with this: Front and mid section joined together by V-bands. Muffler selected was a Borla Pro XS. Below you can see the rear section all welded up with hangers included. Here is how the subframe area looks all mocked up. Pretty clean! A small section was removed to get the bend a bit tighter to the body after we fit everything up. And final fitment with a stainless tip cut at approximately a 10-15 degree slant-cut. Looks awesome and is rock solid! Once that was all buttoned up, the car got rolled into the sun on all fours for the first time since the build began! Looks fantastic in the sun! The maestro himself! Wiring is next!
-
Since we got the car the brake pedal never had any pressure, so now that the suspension was sorted it was time to address the braking system. Ideas for front hardlines were kicked around, but at the end of the day we determined stainless steel softlines would do the job just find and be much more workable. All front lines were custom/hand made out of DOT approved braided lines/fittings and diligently checked over after a good bleed. The results speak for themselves! Below is an example of the fittings/lines used throughout. And all buttoned up! Close up! Clutch master cylinder mounted and its line/bulkhead fitting made. Then the brake master and lines! Here you can see the fitting that goes out to the driver’s side front wheel. And here is what inside the cabin looks like with all the bulkhead fittings and lines. Some aluminum dividers were whipped up to clean things up a bit! After all that, rear softlines were made in a similar manner and everything got bled and checked for leaks. The system was air tight and we finally had a brake pedal! Here’s a nice shot showing all the bling under the car including the front brake line installed.
-
Rear-end time. The plan for this car is to convert to true rear coilovers. First Dad dropped own the crusty old rear end. We have a running theory that the car was semi-submerged at some point, as evidenced by the insane level of crud all over everything. All blown apart and semi cleaned up. No serious rust or damage on the trailing arms and subframe! Differential is unfortunately open with 4:10 ratio. That will be addressed at some point… Subframe getting prepped for weld-in camber and toe adjusters. Super substantial heavy-duty pieces! Got everything all welded in! Trailing arms got cleaned up and painted. Then sleeves for the spherical trailing arm bushings were pressed in and tacked into place. Original Datsun hardware was retained when possible. All bolts were media blasted and coated with high strength clear coat for a pretty cool looking finish. As with the front wheel wells, the entire rear end of the car was stripped of its undercoating, inspected, and repainted in body color. Dad also made up a think sheet aluminum cover to fill the gap between the sliced up fenders and the flares (all the horrific cavity foam was left over PO body work… real high quality stuff…). Results were very satisfying to say the least! And some finished shots! Aluminum panels were riveted in place and sealed up with some seam sealer before paint. Hmmmm whats this? Time for the rear end to go back in. Poly bushings for the subframe and differential mounts. And the money shots…. Rear Wilwood disc conversion! And finally, a little teaser of the rear wheel fitment. You can really see the quality of the paint in body work in these shots as well!
-
Let’s talk about the dash. In these first few photos you can see the dash that came with the car. Basically the bent/twisted and bare frame of the original Datsun dashboard. Reskinning the original dash was an option on the table, but at the end of the day a full custom dash was really the only way to go. Some more CAD work and we had a nice template to work from. Note the gauge placement mock up. Oh look real versions of the printed pictures. Stewart Warner was used for all but one of the gauges. These are period correct gauges and were used in the 510 Trans Am cars. First piece of sheet aluminum cut and shaped. Next the dash face was bent and formed. Some bar stock brackets were fabbed up and tacked together. And and more final fit with gauge mock-up. Note the steering wheel which will eventually be the replacement for the horrific parts store wheel that came with the car. Now let’s cut some holes. Looking good! More to come.
-
Next let’s take a look at some of the interior items. First off, the seats. As this car will be mainly driven on the street, have no rear seat, and a roll bar, the front seats needed to be sporty, but still comfortable enough to drive for long durations and fit multiple drivers/passengers. We never really liked the look of more modern Sparco/Recaro/Bride seat in 510s, and wanted a bit more period correct set of buckets. Like most of us, I browse craigslist daily for deals, and randomly ran across some interesting seats that I had never seen before. They were advertised as vintage rally seats, for less than what most sport seats generally run, so we figured why not! As it turns out, the seats were being sold by a long time car buddy of my Dad who goes back all the way to his white 510 days! Small world stuff. The seats are Paddy Hopkirk Carrera Recliners, a period correct seat designed by Paddy Hopkirk the legendary Irish rally driver. Perfect! Below is a photo that I found of them online before we had them reupholstered. And after being reupholstered. The foam in the center is actually quite compliant so you sink into the seat bottom and the bolsters become much more aggressive/Recaro LS style. The upholstery guy didn’t do exactly what we wanted color wise, but they are definitely acceptable for now and go well with the tan. We haven’t exactly figured out how to incorporate the orange into the rest of the interior but we will probably do something on the door cards to match. A bit of work on some angle aluminum and we have seat mounts! Some new sliders and mounts and the seats fit great. The rear seat delete will be made out of sheet aluminum. After making a couple CAD (cardboard aided design) templates and a homemade sheet metal break we ended up with this: The plain aluminum looked a little boring, so Dad borrowed this beast to help make things a bit more interesting. First test bead rolled! And some bead rolling on the top panel. Much better! These panels will eventually be painted wrinkle black and the large seat back section will get bead rolled as well. Next post we will go over the custom dash setup!
-
Once the bay was looking good, the cast iron (surprisingly somewhat tubular) exhaust manifold was sticking out like a sore thumb in the bay. That got refinished and is looking much better. Also below you can see the DP racing steering box brace installed along with some custom motor mount spacers made from space age material (aka high density cutting board). Then attentions turned to suspension. Everything in the suspension needed replacing, with most of it having the quality of workmanship best illustrated in the following photo: This car will be a dual purpose street/track car, so the plans for suspension were to go with a relatively aggressive setup that could also be streetable. Front end components came from DP Racing and FutoFab and are of excellent quality/fit/finish. First up, chopping up the strut towers to make room for the camber plates. A keen eye will see them all cut out in the painted bay photos from the previous post. Next was to prep the strut tubes for coilovers. Remove the dust shield and spring perches to allow for shortening/welding of the new components. Perches welded on: Strut assembly painted and assembled: Wheel wells were painstakingly stripped of all paint, stich welded where necessary, and undercoating before being painted body color. Finished photos below… Now for the real money shots! Camber plates in: Struts and control arms! Note the massive bumpsteer spacer. And just for fun we fit the new brake setup as well…
-
Great question. There are a few reasons we chose to run the rad setup in its current configuration: 1. There are really no off the shelf and affordable options for radiators with the outlets in the 18RG configuration. This was a $50 radiator that was an oem option. 2. The radiator is dual pass so it has to exit on the far side. 3. We have yet to really prove the longevity/viability of the 18RG. Once we know the motor is good, and we are satisfied with the way it runs/drives there will be an investment in a nicer customer rad with proper outlets.
-
Simon you will have a great time. Best JDM show in SoCal. Not going to make it in the 510 this year but I think I will bring the E30 out! See everyone Saturday.
-
Once the carbs were cleaned, we threw in some new NGK plugs, changed the oil/filter, and fired the car up for the first time in many years! Hearing the throatiness of the dual Mikunis and the rasp from the exhaust was beautiful to experience. I think we have a video somewhere of that first start which I will try to get uploaded… Now that we knew it was a runner, it was time for more work to really move forward. First we test fit some trumpets on the carbs for fun… This car will have foam air filters, but the open trumpets are just so damn cool. In these photos you can also see the simpler single outlet water neck that was from some type of 80s Toyota that aided in cleaning things up. Next we took a look at the radiator setup. The 18RG has its radiator outlets on the opposite side as the factory 510 configuration, and the previous owner’s original swap radiator setup was full of garbage 90s parts store components. Perfect opportunities for upgrades. After a bit of searching, we found an OEM VW radiator would fit the bill for the slightly awkward setup. The upper and lower hose were a combination of tubing/hoses that got the setup to be much more robust. After a couple bends on some aluminum for brackets and a beauty cover, this was the result: Now you might have noticed a bit of paint in the engine bay in those last few radiator photos. The entire bay was prepped and painted in body color tan and wow, did it make a huge difference. Much more to come! :D
-
On a trip home from Spring Mountain Raceway in Nevada, Dad stopped in at BRE to get the car certified as a BRE tribute car. So awesome! Back home and back to work. With paint and body in a good place, it was time to tackle the 18RG. The engine turned over smoothly, so we were hopeful it wouldn’t take a ton of effort get the thing to fire up. Below are a few reference photos I took of the engine before initial tear down. First step was to completely go through the twin 40mm Mikunis that had definitely seen better days. The amount of fuel varnish in the bowls/jets was laughable, and we even found a few surprises as we disassembled and cleaned. Multiple hours of cleaning/rebuilding yielded impressive results. Left is done, right is still to be cleaned and rebuilt.